Smart Mobility & Building
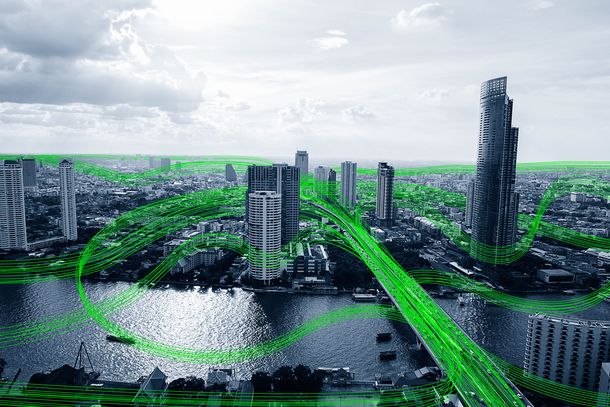
Dieser Forschungsschwerpunkt an der Hochschule Bochum fokussiert auf Smart-City-Ansätze und insbesondere auf smarte Lösungen für die Mobilitäts- und Bausektoren. Die Forschenden entwickeln ressourceneffiziente Mobilitätskonzepte und moderne Gebäudeinfrastrukturen als Bausteine einer nachhaltigen Verkehrs- und Energiewende auf Quartiers- und Stadt(teil)ebene. Dies umfasst auch Projekte zu lokal autarker Energieversorgung oder Speichertechnologien. Etablierte Themenfelder sind die Entwicklung von Solarfahrzeugen und die Erforschung von Elektromobilität und innovative digitale Methoden wie Building Information Modeling (BIM). Die Forschungsprojekte sind dabei national, aber auch stark europäisch und international ausgerichtet.
Der Forschungsschwerpunkt profitiert von der Zusammenarbeit professuren- oder fachbereichsübergreifender Einrichtungen an der Hochschule Bochum, wie dem Institut für Elektromobilität, dem Interdisziplinären Institut für Angewandte KI und Data Science Ruhr (AKIS), dem BIM-Institut (Building Information Modelling), dem Labor für Nachhaltigkeit in der Technik und dem Institut für Mobilität und Verkehrssysteme.
Im Einklang mit dem Nachhaltigkeitsprofil der Hochschule stehen Innovationen, die sich auf die Sustainable Development Goals (SDGs) beziehen, besonders im Vordergrund. Der Fokus liegt auf inter- und transdisziplinären Lösungen, die angewandte Forschung nutzen, um Antworten auf dringende globale Herausforderungen zu finden, sowie auf nachhaltigen lokalen und regionalen Lösungsansätzen, die bevorzugt den gesamten Lebenszyklus der entwickelten Ansätze und Innovationen betrachten und nachhaltigen individuelles Verhalten fördern.
Laufende Projekte zu Smart Mobility & Building
Projektleitung: Prof. Dr.-Ing. Friedbert Pautzke und Tobias Scholz, M.Sc.
Fördermittelgeber: Bundesministerium für Bildung und Forschung (BMBF)
Projektträger: Bundesinstitut für Berufsbildung (bibb)
Förderprogramm: InnoVET
Laufzeit: 2024 - 2027
Herausforderung
Der Bedarf an Fachkräften im Handwerk und in der Industrie, die sich mit Batterietechnologien, Elektromobilität und Wasserstoffsystemen auskennen, steigt stetig. Um die Energie- und Mobilitätswende erfolgreich zu gestalten, müssen sich diese Fachkräfte weiterbilden, um innovative Technologien entwickeln und umsetzen zu können.
Lösung
Aufgabe des InnoVET Plus-Projekts TraFuSMS ist es, ein modulares Bildungskonzept zu entwickeln, das die bedarfsorientierte Aus- und Fortbildung von Fachkräften für die Energie- und Mobilitätswende ermöglicht. Im Mittelpunkt stehen drei Module für Fachkräfte aus Kfz-Betrieben und der Industrie sowie Mitarbeitende von Start-ups und kleineren Betrieben im Bereich nachhaltiger Mobilität:
- Bewertung von Batterien in Elektrofahrzeugen: Dieses Modul befähigt Lernende und Unternehmen, Diagnose- und Instandsetzungsmaßnahmen an Elektrofahrzeugen und deren Energiespeichern durchzuführen.
- Innovationsmanagement in kleinen Unternehmen: Hier wird das unternehmerische und innovationsorientierte Verhalten der Mitarbeitenden innerhalb des Betriebes gefördert.
- Arbeiten an Wasserstoffsystemen und Entwicklung nachhaltiger Energiesysteme: Lernende werden auf das sichere Arbeiten an Wasserstoffsystemen vorbereitet und erhalten das Wissen, um verschiedene Energiesysteme und Mobilitätslösungen hinsichtlich ihrer Nachhaltigkeit zu bewerten.
Der modulare Aufbau der Qualifizierung ermöglicht auch Mitarbeitenden in Start-ups oder kleineren Betrieben die Teilnahme, ohne längere Abwesenheiten im Unternehmen zu verursachen.
Zudem wird die Nutzung intelligenter, KI-basierter Übersetzungssoftware erprobt, um die Inhalte durch englischsprachige Fachbegriffe zu erweitern und somit die Lernenden auf Dokumentationen in englischer Sprache vorzubereiten.
Transfer
Das Lernangebot soll nach erfolgreicher Erprobung durch die Handwerkskammer Dortmund (HWK), der Bochumer KFZ-Innung (KFZI) und der regionalen Industrie- und Handelskammer (IHK) zertifiziert werden. Diese Zertifizierung stärkt die Verstetigung und Anerkennung der Konzepte in der Branche.
Die entwickelten Lerninhalte sollen nach Projektende als Bildungsangebote oder zur Ergänzung der Ausbildung bei der Handwerkskammer und der Innung für Kfz-Gewerbe aufgenommen werden. Darüber hinaus bieten die technischen Lehrmodule direkte Anknüpfungspunkte zur Energiebranche, da Energiespeicher aus Kraftfahrzeugen als dezentrale Netzspeicher in Haushalten und der Industrie weiterverwendet werden.
Konsortium
- Hochschule Bochum
- Institut für Elektromobilität
- DigiTeach Institut
- Resort Studium, Lehre und Weiterbildung
- Handwerkskammer Dortmund
- KFZ-Innung Bochum
Assoziiert
- IHK Mittleres Ruhrgebiet
- Bochum Wirtschaftsförderung
- Weitere: Voltvogel, E-Adventures, ruhrvalley, Nüwiel
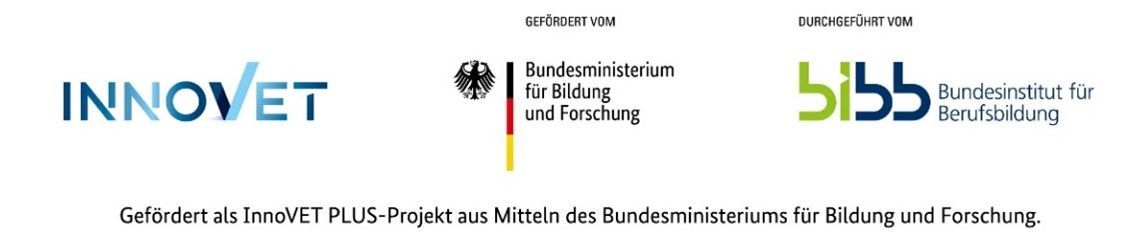
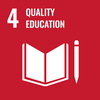
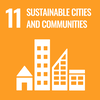
Projektleitung HSBO: Prof. Dr.-Ing. Iris Mühlenbruch, Prof. Dr.-Ing. Sebastian Seipel
Fördermittelgeber: Land NRW
Laufzeit: 2024-2034 (Zeitraum Landesförderung)
Die Förderung des Radverkehrs ist ein Schlüsselelement der nachhaltigen Mobilität und daher ein wichtiges Anliegen der Hochschule Bochum. Angesichts des aktuellen Fachkräftemangels, der die Planung und den Bau von Radverkehrsanlagen erschwert, wird an der Hochschule Bochum eine neue Fahrradprofessur eingerichtet. Gefördert wird diese Professur vom Land NRW, um die Ausbildung dringend benötigter Fachkräfte zu unterstützen und die Verkehrswende voranzutreiben.
Die Förderung umfasst eine Laufzeit von zehn Jahren und stellt jährlich bis zu 400.000 Euro zur Verfügung. Die Mittel beinhalten neben der Finanzierung der Professur selbst auch die Anstellung von zwei wissenschaftlichen Mitarbeitenden. Diese Ressourcen ermöglichen es der Hochschule Bochum, die Forschung und Lehre im Bereich des Radverkehrs zu erweitern und gleichzeitig einen wichtigen Beitrag zur Ausbildung neuer Fachkräfte auf akademischem Niveau zu leisten.
Ein wesentlicher Bestandteil der Förderung ist die Einrichtung eines Fahrradlabors, das durch die Landesmittel realisiert wird. Dabei liegt das Augenmerk auf der Erweiterung des Konsortiums an Erhebungs- und Messgeräten, um sicherzustellen, dass Theorie und Praxis in Lehre und Forschung eng miteinander verknüpft sind. Die Studierenden und Forschenden werden hier die Möglichkeit haben, innovative Lösungen für die Radinfrastruktur nicht nur zu entwickeln, sondern auch unter realen Bedingungen zu testen.
Zusätzlich zur Einrichtung des Fahrradlabors plant die Hochschule Bochum die Anschaffung von Materialien für sogenannte Reallabore. Diese Reallabore sind von großer Bedeutung, da sie es ermöglichen, theoretisch erarbeitete Konzepte praktisch zu testen und damit den Bezug zur Praxis zu stärken. Darüber hinaus fungieren Reallabore als Schnittstelle zwischen Forschung und Bevölkerung, indem sie Bewusstsein und Akzeptanz für innovative Lösungen im Bereich der Radinfrastruktur schaffen. Hierdurch wird die Bevölkerung aktiv in die Entwicklung und Umsetzung neuer Verkehrskonzepte eingebunden.
Neben der intensiven Arbeit in Lehre und Forschung an der Hochschule Bochum sind Kooperationen mit umliegenden Kommunen, insbesondere der Stadt Bochum, ein weiterer zentraler Aspekt des Projekts. Durch diese Zusammenarbeit sollen praxisorientierte Lösungen entwickelt und direkt in den beteiligten Gemeinden umgesetzt werden. Diese Vernetzung bietet nicht nur den Studierenden wertvolle Praxiserfahrungen, sondern ermöglicht es auch den Kommunen, von den neuesten wissenschaftlichen Erkenntnissen zu profitieren und innovative Radverkehrslösungen vor Ort zu realisieren.
Mit der Einrichtung der Fahrradprofessur und den damit verbundenen Maßnahmen setzen die Hochschule Bochum und das Land NRW einen bedeutenden Impuls für die Verkehrswende und leisten einen wichtigen Beitrag zur Ausbildung von Fachkräften im Bereich des Radverkehrs. Dies stellt einen relevanten Meilenstein auf dem Weg zu einer nachhaltigen Mobilität und einer zukunftsfähigen Verkehrsinfrastruktur dar.
Weiterführende Links:
Projektleitung: Prof. Dr.-Ing. Jutta Albus
Fördermittelgeber: Zukunft Bau Forschungsförderung, Bundesinstitut für Bau-, Stadt- und Raumforschung
Laufzeit: Okt 2023 - Okt 2025
Weitere Projektpartner:
Bundesverband der Deutschen Ziegelindustrie e.V.
Gipsbauplatten haben mit einer Produktion von über 233 Mio. m² pro Jahr in Deutschland einen maßgebenden Einfluss auf den Gipsverbrauch mit steigender Tendenz. Die Verfügbarkeit von Gips nimmt mit der zunehmenden Schließung von Kohlekraftwerken (80 % sind REA-Gips) und der sinkenden Verfügbarkeit aus Primärlagerstätten drastisch ab. Somit ist eine alternative Bauweise zur Errichtung nichttragender Innenwände mit geringem CO2 Footprint sowie Energiebedarf zur Herstellung unter Nutzung regionaler und nachwachsender Materialressourcen dringend erforderlich. Mittels des anvisierten Forschungsvorhabens soll ein Beitrag zur ressourceneffizienten Kreislaufwirtschaft und zur Ressourcenschonung geleistet, und der Einsatz rohstoffintensiver Verfahren vermieden werden. Gleichzeitig zielt das Projekt darauf ab, bautechnische Verbesserungen (baukonstruktiv, bauphysikalisch) zur Einsparung des betrieblichen Energiebedarfs im Neu- und Bestandbau zu erreichen. Das Forschungsvorhaben untersucht die Entwicklung von Hochlochlehmbausteinen zum einen auf Werkstoffebene. Dabei stehen materialtechnische Eigenschaften im Hinblick auf die Realisierung eines maßhaltigen, dauerhaften und kreislauffähigen Produkts
durch den Einsatz natürlicher, nachhaltiger Zusatzstoffe sowie die Anpassung des Herstellverfahrens im Fokus. Zum anderen wird der Einsatz der Hochlochlehmbausteine im Hinblick auf baukonstruktive Anforderungen überprüft. Aspekte wie Fügung der Bausteine, Montage, Verputzen und Rückbau sowie architektonische Gestaltungsmöglichkeiten werden auf Potentiale, ggf. Einschränkungen für Neu- und Bestandsbauten auch während der Betriebsphase untersucht und mittels Lebenszyklusanalyse überprüft. Der Baustoff Lehm birgt ein hohes Kreislaufpotential. Um den drängenden Fragen nach zukunftsfähigen Lösungsansätzen im Bauen nachzukommen, wird eine alternative Herangehensweise zur konventionellen Trockenbauwand auf Grundlage einer ressourcensparenden, zirkulären Bauweise etabliert.
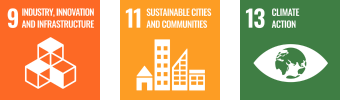
Projektleitung: Prof. Dr.-Ing. Jutta Albus
Fördermittelgeber: DBU Deutsche Bundesstiftung Umwelt
Laufzeit: 2022-2024
Das Forschungsprojekt stellt die Entwicklung von vorgefertigten Bauteilen oder Baugruppen in Hybridbauweise in den Fokus, die basierend auf einem durchgängig digitalen Planungs- und Produktionsprozess eine höhere konstruktive Flexibilität und gestalterische Varianz erreichen, und damit zur Verbesserung der nachhaltigen Nutzung von Gebäuden beitragen. Ausgehend von einem adaptiv-assoziativen Bausystem werden vorgefertigte, dreidimensionale Raummodule aus Boden und Wand (z.B. U-Element oder L-Element aus Beton) mit linearen Tafelelementen(Wand/Boden/Decke-Elemente aus Holz, Stahl, Beton oder Holz-Beton-Verbund) und punktförmigen Elementen (Stützen etc.) systematisch in einer Planungsleistung kombiniert und im Hinblick auf eine automatisierte Produktion baukonstruktiv entwickelt, sodass eine große Bandbreite an Lösungsansätzen für mehrgeschossige Gebäudetypologien ermittelt werden kann. Alleinstellungsmerkmal des Forschungsansatzes ist der komplementäre Mittelweg aus Raummodul- und Elementbauweise im Hinblick auf eine offene, adaptive Bauweise, die dem komplexen Anforderungsgeflecht heutiger Planungsaufgaben durch eine hohe Flexibilität sowohl in der materialkonstruktiven Ausführung als auch der gestalterischen Varianz entspricht.
Dabei zielt die Forschungsleistung insbesondere auf eine Systemoffenheit ab. Für ein „nachhaltig offenes System“ muss eine Balance zwischen Flexibilität und damit einer Adaptivität auf der einen Seite und Systematisierung auf der anderen Seite gefunden werden, so dass eine Anwendbarkeit sowohl im Bestand als auch im Neubau möglich ist.
Standardisierte, seriell gefertigte Elemente bilden die Grundlage einer Bauweise, die durch sparsamen Materialeinsatz und reversible Fügungen individualisierbare architektonische Lösungen realisierbar macht. Die Schnittstelle zwischen digitalem Gestalten und automatisierter Fertigung bildet in diesem Zusammenhang einen Schwerpunkt.
Um die genannten Anforderungsparameter einer Bauaufgabe in den Planungsprozess zu überführen, miteinander in Beziehung zu setzen und diese schließlich für den Planer zugänglich zu machen, wird ein Projekt über ein digitales Entwurfswerkzeug im Sinne eines ganzheitlichen Prozesses vorbereitet (digitale Gestaltung von Prozessen) und über die einzelnen Leistungsphasen bis hin zur (teil-)automatisierten Fertigung (Automatisierung der Fertigungstechnologie) ausgearbeitet. Eine neuartige, digitale Planungsmethodik ermöglicht die Kombination von dreidimensionalen (Raum-)Einheiten mit zweidimensionalen Komponenten als offene Konstruktionstypologie.
Somit schließt das zukunftsfähige Konzept erfolgreich die existierende Lücke zwischen Planung und Produktion. Durch die Neugestaltung einer Prozessstruktur, deren Schwerpunkt in der digitalen Verknüpfung von Planungsparametern liegt, entsteht ein präziser Datenaustausch, der sowohl die Planer bei der Entscheidungsfindung unterstützt als auch die Ineffizienz tradierter Abläufe in der Produktion überwindet.
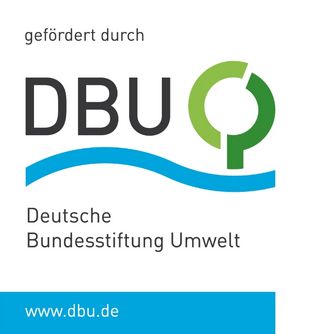
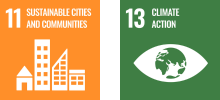
Projektleitung: Prof. Dr.-Ing. Jutta Albus
Fördermittelgeber: Zukunft Bau Forschungsförderung / Bundesinstitut für Bau-, Stadt- und Raumforschung (BBSR) im Bundesamt für Bauwesen und Raumordnung
Laufzeit: 10/2023-09/2025
Die Senkung des Energiebedarfs im Wohnungsbestand Deutschlands ist eine zentrale Aufgabe der nächsten Jahre. Dazu muss die Sanierungsquote rapide gesteigert werden. Hierfür benötigt es kostengünstige und materialsparende Lösungen. In einer umfassenden Untersuchung wird der Lebenszyklus typischer Bestandswohngebäude betrachtet. Dabei werden, anders als üblich, auch die am konkreten Standort vorhandenen Optionen der Energieversorgung, die graue Energie der Baumaßnahmen sowie der Aufwand für den Betrieb und - bisher noch kaum beachtet - die Bandbreite des zu erwartenden Nutzerverhaltens berücksichtigt. Der Energieverbrauch wird zu diesem Zweck über thermische Simulationen ermittelt. Dieser Methode liegt die These zugrunde, dass durch diese ganzheitliche Betrachtung, die das Nutzerverhalten und den Einsatz für Technik und Betriebsenergie mit betrachtet, Sanierungslösungen gefunden werden können, die in der Praxis wirksam den Energiebedarf senken. Die Forschenden erwarten dabei Sanierungslösungen, die weniger kosten, aber im Vergleich zu einer EH55 Sanierung, genauso viel CO2 einsparen. Dadurch wird die vorhandene Leistungskraft der Bauwirtschaft auf viele kleinere, ökologisch und ökonomisch sinnvolle Maßnahmen verteilt und so größere Fortschritte bei der CO2-Einsparung ermöglicht. Gepaart mit den richtigen Anreizen aus der Politik und einem konsequenten Umbau der Energieversorgungsstruktur könnten die gesteckten Ziele damit erreichbarer werden. Die Ergebnisse werden, ähnlich wie beim Vorgängerprojekt "Einfach Bauen", als Leitfaden in leicht verständlicher Form für Interessierte zusammengefasst.
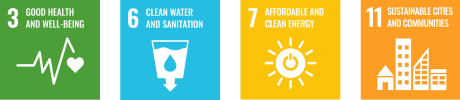
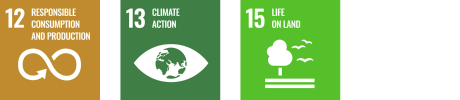
Projektleitung: Prof. Dr.-Ing. Jutta Albus
Fördermittelgeber: DBU Deutsche Bundesstiftung Umwelt
Laufzeit: 2022-2024
Angesichts der brennenden ökologischen Fragen unserer Zeit kann sich der Planungs- und Bausektor nicht mehr damit zufriedengeben, den negativen Einfluss der Bautätigkeit zu minimieren. Vielmehr muss das visionäre Ziel von positiven Gebäuden und Quartieren verfolgt werden, um den ökologischen Wandel im Gebäudesektor zu beschleunigen. Das Forschungsprojekt soll in diesem Kontext eine ehrliche Definition des „positiv Bauens“ generieren, bei der möglichst viele Handlungsfelder betrachtet und deren Wechselwirkungen kritisch analysiert werden. Auch Grenzen des positiven Bauens sollen transparent dargestellt werden.
Im Rahmen des Forschungsprojektes werden folgende Handlungsfelder differenziert bearbeitet: Material, Energie, Wasser, Grün, Gesellschaft und Mobilität. Die gleichzeitige Berücksichtigung der genannten sechs Handlungsfelder bietet ein enormes Potenzial, um die Nachhaltigkeitsziele im Bauwesen zu erfüllen. Damit werden Synergieeffekte genutzt, die sich aus der integrierten Betrachtung der einzelnen Bereiche ergeben.
Bestehende Umsetzungsstrategien dienen als Grundlage, um neue, innovative Lösungsansätze zu entwickeln und auf ihre Tauglichkeit im Kontext von geplanten Quartiersentwicklungen zu bewerten. Wenn die entwickelten Lösungsansätze zur Erreichung des definierten Ziels geeignet sind, werden sie in einen Handlungsleitfaden übernommen, um neue Projekte ganzheitlich zu verwirklichen, in allen Handlungsfeldern weitestgehend positive Umweltwirkungen zu generieren und dabei bezahlbaren Wohnraum zu schaffen. Um die Zieleinhaltung stetig im Planungsprozess zu überprüfen und Entscheidungsprozesse zu lenken, wird weiterhin ein multikriterielles Bewertungstool aufgesetzt.
Zur Validierung der Handlungsempfehlungen und des Bewertungstools wird das Forschungsprojekt an ein konkretes Praxisprojekt, ein neues Quartier bei Bamberg, gekoppelt und mit Praxispartnern umgesetzt. Der Fokus liegt dabei auf der Planungsphase, die wissenschaftlich begleitet werden soll. In enger Abstimmung zwischen den Forschenden und den Planungsbeteiligten des Praxisprojekts werden Umsetzungsstrategien zum Bauen mit positiven Umweltwirkungen für die oben genannten Handlungsfelder integrativ erarbeitet, entwickelt und im Hinblick auf die Übertragbarkeit auf weitere Projekte aufbereitet, damit diese für ähnliche Folgeprojekte anwendbar und nutzbar sind. Bei zukünftigen (Wohnungs-) Neubauten sollen somit die Potenziale eines möglichst positiven Bauens in Bezug auf Material, Energie, Wasser, Grün, Gesellschaft und Mobilität genutzt werden können, anstatt negative Umweltwirkungen des Bauens nur zu reduzieren.
Das Forschungsprojekt leistet somit einen Beitrag zur Umsetzung und Weiterentwicklung des „Regenerative Designs“ auf Gebäude- bzw. Quartiersebene mit dem Ziel, Strategien für die Umsetzung von in ökologischer und sozialer Hinsicht positiven Bauweisen aufzuzeigen.
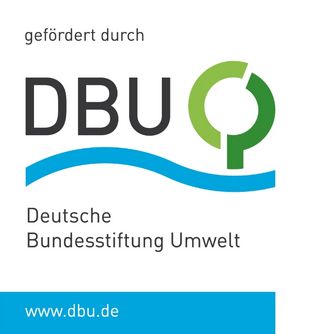
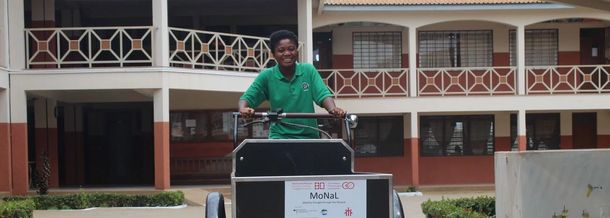
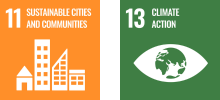
Projektleitung: Prof. Dr.-Ing. Semih Severengiz
Fördermittelgeber: Bundesministerium für Umwelt, Naturschutz und nukleare Sicherheit (BMU)
Laufzeit: 08/2020 – 03/2023 (verlängert)
MoNaL zielt darauf ab, nachhaltige Mobilitätslösungen für Länder in Subsahara-Afrika zu etablieren. Das vom BMU im Rahmen des Programms "Exportinitiative Umwelttechnologien" geförderte Projekt (mit einem Zuschuss von 397.382,00 €) berücksichtigt umfassend die gesamte Lebenszykluswirkung – von der Fahrzeugproduktion und -gestaltung bis hin zur Energieversorgung und zum Recycling von Fahrzeugen und Energieinfrastruktur. Eine Pilotumsetzung in Ghana, am Standort des lokalen Partners Don Bosco, beinhaltet den Test eines Systems zur Vermietung von Elektromopeds und Lastenrädern. Diese Initiative passt sich den lokalen Bedingungen und Benutzeranforderungen an. Nachhaltige Mobilität ist mit erneuerbarer Energie verbunden, was zur Entwicklung eines intelligenten Mini-Netzes führt, das von unabhängigen Solarinstallationen und Ladestationen betrieben wird.
Das Mini-Netz, ein Bestandteil des Projekts, verfügt über eine automatische Abrechnung, die Echtzeitanpassungen der Strompreise ermöglicht, basierend auf Faktoren wie Angebot, Nachfrage, Wetter und Batteriestatus. Das Ziel ist es, die Nutzung nachhaltiger Mobilitätsalternativen zu intensivieren, unter Berücksichtigung eines zuverlässigen und nachhaltigen Zugangs zu Energie. Um das Problem des Elektroschrotts im Zielland anzugehen, bezieht das Projekt die End-of-Life-Phase des entwickelten Produktsystems mit ein. Es umfasst die Analyse bestehender Recyclingstrukturen in Ghana, die Erkundung von Optionen für Zweitverwendungen von Solarmodulen und Batterien, die Organisation von Workshops mit lokalen Interessengruppen zur Entwicklung von Umweltstandards sowie Schulungen in Recycling und Upcycling. Qualifizierungsmaßnahmen in den Bereichen Elektromobilität, Solartechnologie und Recycling gewährleisten die nachhaltige Nutzung des Produkts.
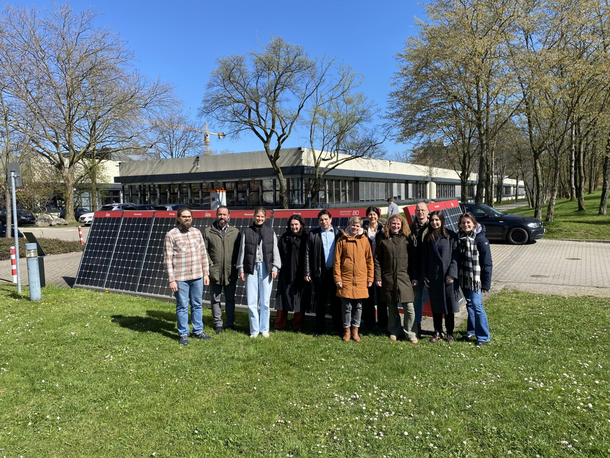
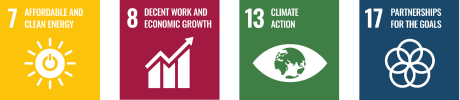
Projektleitung: Prof. Dr.-Ing. Semih Severengiz
Fördermittelgeber: Europäische Kommission
Volumen (in €): 321.911
Laufzeit: 06/2022 – 05/2026
Innovative Berufsbildung im Zeitalter des Energiemodus SEED (Sustainable Energy Education) ist eine Zusammenarbeit zwischen fünf europäischen Regionen unter der Leitung der Fachhochschule Utrecht. Das Ziel ist die Schaffung eines fossilfreien Kontinents durch herausragende, innovative berufliche Ausbildung.
SEED setzt sich für die entscheidende Rolle der Bildung im Kampf gegen den Klimawandel und den Übergang zu grüner Energie ein. Das Projekt fördert die gemeinsame Entwicklung herausragender Energiebildung an Berufseinrichtungen und regionalen Akteuren mit dem Ziel, qualifizierte Fachleute zu vermehren, Studiengänge mit dem Arbeitsmarkt zu integrieren und neue Energietechnologien voranzutreiben.
Die Initiative gründet fünf Exzellenzzentren für berufliche Bildung in den Niederlanden, Finnland, Spanien, Deutschland und Griechenland und bildet eine internationale Gemeinschaft, die Standards und Einblicke in die nachhaltige Energiebildung teilt.
Zusätzlich rüstet SEED, Teil des CoVE-Programms, das von Erasmus+, der EU finanziert wird, Einzelpersonen mit zukunftsorientierten Fähigkeiten aus und stärkt die regionale Innovation. Es unterstützt bewährte Praktiken in Lehre, Industriepartnerschaften und Bildungsmanagement, um die Attraktivität der beruflichen Bildung zu steigern.
CoVEs, von der Europäischen Kommission eingeführt, sind Netzwerke, die berufliche Praktiken aktualisieren und hochwertige Fähigkeitsschulungen bieten, die mit regionalen Entwicklungsstrategien verknüpft sind, um neue Synergien und Wissensschaffung zu fördern.
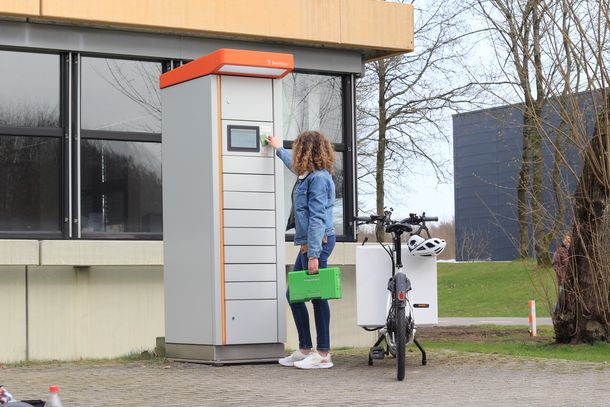
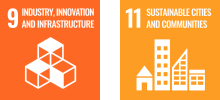
Projektleitung: Prof. Dr.-Ing. Semih Severengiz
Fördermittelgeber: Bundesministerium für Bildung und Forschung (Förderkennzeichen: 13FH0I03IA)
Volumen (in €): 419.600
Laufzeit: 07/2022 – 07/2024
Der Verkehrssektor befindet sich in einer umfassenden Transformation, die darauf abzielt, Treibhausgasemissionen und Luftschadstoffe zu reduzieren sowie digitale, intelligente Lösungen für Ressourcen- und Flächeneffizienz in städtischen Gebieten zu entwickeln. Lösungen müssen nachhaltig und erschwinglich sein. Leichtelektrofahrzeuge (LEVs) wie E-Scooter, Pedelecs, Lastenräder und E-Mopeds sind entscheidend für energieeinsparende, emissionsfreie städtische Mobilität.
Das Projekt erforscht nachhaltige Energieversorgung für LEVs und geht dabei der Herausforderung nach, diese Fahrzeuge mithilfe digitaler Lösungen in erneuerbare Energiequellen zu integrieren. Es baut auf dem Teilprojekt SCiSusMob I auf und betont einen ganzheitlichen Ansatz zur Mobilität und Energie aus nachhaltiger Perspektive, unter Einbeziehung zukunftssicherer digitaler Infrastrukturen. Das Ziel ist es, Forschungsergebnisse in einem realen Labor zu testen und zu validieren, wobei der Fokus auf einer einheitlichen Plattform für Mobilitäts- und Energiedienstleistungen liegt. Dies führt zu einer standardisierten Methodik zur Bewertung der Nachhaltigkeitsauswirkungen von Mobilitätsdienstleistungen.
Hauptforschungsbereiche umfassen:
Entwicklung von Nachhaltigkeitsbewertungsmethoden wie der Ökobilanz (LCA) und Akzeptanzstudien. Untersuchung von Energieversorgungskonzepten für LEVs. Erstellung von Geschäfts- und Betriebsmodellen für Mobilitäts- und Energiedienstleistungen. Gestaltung einer dezentralen digitalen Plattform für diese Dienstleistungen. Erprobung des Mobilitäts- und Energiesystems in einer realen Umgebung. Etablierung von Standards und rechtlichen Rahmenbedingungen. Unter der Leitung von Prof. Dr.-Ing. Semih Severengiz ist das Projekt eine Zusammenarbeit mit Unternehmen aus den Bereichen Energie und Mobilität und wird von Firmen wie e-bility GmbH, Stadtwerke Bochum Holding GmbH und anderen unterstützt, die Drittmittel bereitstellen.
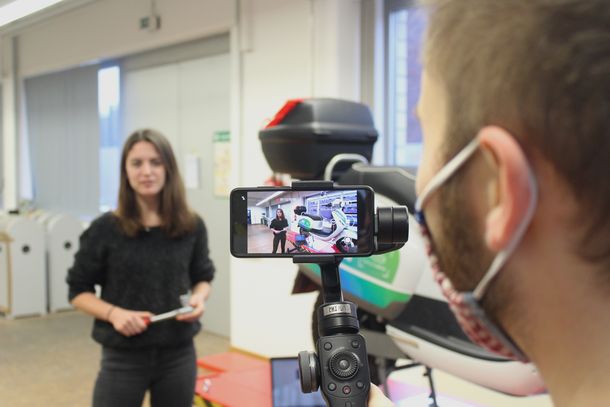
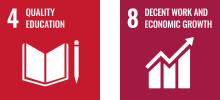
Projektleitung: Prof. Dr.-Ing. Semih Severengiz
Fördermittelgeber: Bundesministerium für Bildung und Forschung (Förderkennzeichen: 21IV009F)
Volumen (in €): 395.794,12
Laufzeit: 12/2020 – 11/2024
Kooperationspartner: hier finden Sie eine Liste der Kooperationspartner.
Das InnoVET-Projekt UpTrain konzentriert sich darauf, die berufliche Bildung im kaufmännisch-technischen Sektor der Mobilitätsindustrie zu revitalisieren. Angesichts des Bedarfs an 100.000 zusätzlichen qualifizierten Mitarbeitern im öffentlichen Verkehr bis 2025 reagiert das Projekt auf Herausforderungen in den Bereichen Digitalisierung, Elektrifizierung und Automatisierung.
UpTrain zielt darauf ab, die Durchlässigkeit und Attraktivität der branchenspezifischen Ausbildung durch digitale Lernmaterialien für eine Mobilitätsakademie und tripartite Fortbildungsprogramme, die Verkehrsunternehmen, Universitäten und die Industrie verbinden, zu verbessern. Das Projekt wird umfassende Weiterbildungsmodelle für den öffentlichen Verkehrssektor entwickeln und testen.
Das Labor für Nachhaltigkeit in der Technik der Fachhochschule Bochum wird kooperative Lernsequenzen in den Bereichen Energie, neue Mobilitätslösungen und Szenariotechniken verbessern, digitale Inhalte mit Blended-Learning-Ansätzen integrieren. Die Hochschule trägt auch zu länderübergreifenden Bildungsberatungsdiensten bei und beteiligt sich an der Projektbewertung und -verbreitung.
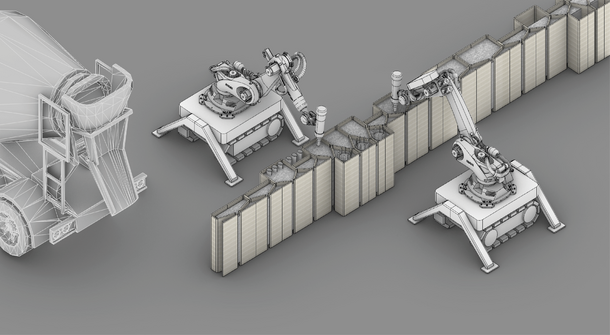
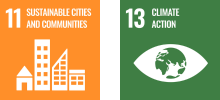
Projektleitung: Prof. Sven Pfeiffer
Fördermittelgeber: Bundesministerium für Wirtschaft und Klimaschutz (BMWK)
Laufzeit: 03/2022 – 02/2025
Das Ziel des Projekts 3DLight_OnSite besteht darin, die CO2-Emissionen in der Bauindustrie zu reduzieren, indem ein durchgängig CO2-optimierter digitaler Workflow zur Herstellung multifunktionaler Leichtbauteile mit gradienten Eigenschaften entwickelt wird. Die Hauptinnovation besteht darin, Leichtbau im Baubereich durch die Konzeption, Entwicklung und Prüfung der ortsbasierten Herstellung in der additiven Fertigung einzuführen. Es werden Materialien und digitale Planungsmethoden für personalisierte, multifunktionale Leichtbauteile entwickelt, die mithilfe von robotergestützten additiven Verfahren hergestellt werden. Das Projekt überbrückt die Lücke zwischen Grundlagenforschung und industrieller Anwendung, indem die Ergebnisse mit Referenzkomponenten aus der Praxis getestet und validiert werden.
Für weitere Informationen zu diesem Projekt: 3DLight_OnSite
Projektleitung: Prof. Dr.-Ing. Friedbert Pautzke
Fördermittelgeber: Bundesministerium für Bildung und Forschung, Programm FH-Impuls
Laufzeit: 04/2022 – 03/2024
Mithilfe der Konzipierung eines modularen Experimentierfahrzeugs und Erzeugung Digitaler Zwillinge soll ein breites Spektrum an verfügbaren und kombinierbaren Antriebskomponenten für elektrische Fahrzeugantriebe erzeugt werden, um so den Integrationsaufwand planbar gering zu halten.
Ziel des Projekts: Erzeugung eines breiten Spektrums von verfügbaren und kombinierbaren Antriebskomponenten für elektrische Fahrzeugantriebe, um den Integrationsaufwand planbar gering zu halten.
Dafür soll im explorativen Projekt OMAx-Vehicle ein modulares Experimentierfahrzeug konzipiert werden, das die Kompatibilität und Kommunikation elektrischer Komponenten von unterschiedlichen Herstellern in unterschiedlichen Leistungsklassen ermöglicht.
Um dieses Vorhaben in seiner Komplexität möglichst effektiv und lösungsorientiert umzusetzen, wird der methodische Ansatz des Modellbasierten Systems Engineerings (MBSE) gewählt. Dabei werden aus den bereits vorhandenen realen mechatronischen Systemen des elektrischen Antriebs (OMEx-DriveTrain) disziplinspezifisch und disziplinübergreifend digitale Zwillinge erzeugt. Die realen Objekte und Prozesse werden dabei nicht einfach „nur“ digital abgebildet, das DigitaleZwillings-Konzept stellt den Anspruch eine Kommunikation von Daten und Informationen zwischen realen und virtuellen Objekten/Prozessen zu erzeugen.
Ergebnisse des Projekts sind also:
- Konzipierung eines modularen Fahrzeugaufbaus mit Antriebsstrang
- Die praktische Anwendung von MBSE
- Die Definition von Simulationsmodellen zur Abbildung von digitalen Zwillingen
- Die Erzeugung von digitalen Zwillingen der Antriebskomponenten
- Reelle Erweiterung der OMEx-DriveTrain-Plattform um die Brennstoffzellentechnologie
- Hybrides Testen, Datenerfassen und Analysieren mit X-in-the-Loop
- Schulungsunterlagen, Tutorials und Beispiele/Demos als Online-Material
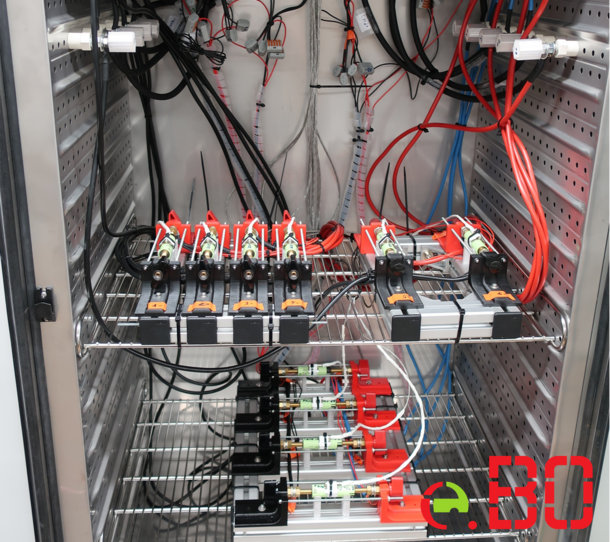
Projektleitung: Prof. Dr.-Ing. Friedbert Pautzke
Fördermittelgeber: Bundesministerium für Bildung und Forschung (BMBF), Initiative "Battery 2020 Transfer"
Laufzeit: 11/2022 – 11/2025
UniZuB konzentriert sich auf die Entwicklung, Prüfung und Optimierung von Software- und Hardwarelösungen zur Bewertung des Zustands (State of Health; SOH) von Hochvoltbatterien (HV-Batterien). Hierbei werden Computersimulationen und praktische Experimente kombiniert, um die Anwendbarkeit im Feld zu gewährleisten.
Der Zustandsschätzer, auch als Diagnosewerkzeug oder Batterietester bezeichnet, wird in Zusammenarbeit mit Industrie- und Forschungspartnern über drei Jahre mithilfe der transdisziplinären Design-Thinking-Methode entwickelt. Zu den Schlüsselindustriepartnern gehören AVL DiTEST GmbH, spezialisiert auf HV-System-Messgeräte, und Zweidenker GmbH, Experten für Cloud-Lösungen. Das Projekt bezieht auch die AWG Abfallwirtschaftsgesellschaft mbH Wuppertal ein, die das Werkzeug für Entscheidungen bezüglich "Second-Life vs. Recycling" von HV-Batterien interessiert.
Das Projekt zielt darauf ab:
- Eine schnelle, zuverlässige und anpassbare Methodik zur Abschätzung des Zustands von HV-Batterien zu entwickeln.
- Einen Demonstrator für ein universelles Schnelldiagnosegerät für HV-Batterien zu erstellen, einschließlich Machbarkeitsnachweis.
- Cloud-Lösungen zur Speicherung verschiedener Arten von Daten zu entwickeln.
- Eine nachhaltige Wertschöpfungskette für HV-Batterien (Kreislaufwirtschaft) zu realisieren.
- Den Wissens- und Technologietransfer für Lebenszyklusanalysen von HV-Batterien zu erleichtern.
- Eine einheitliche Methodik für die Gefährdungsbeurteilung beim Transport von Elektrofahrzeugen und beim Batterierecycling zu etablieren.
Zu den akademischen Partnern gehören das Institut für Elektromobilität der Fachhochschule Bochum, Neue Effizienz gGmbH (ein Institut der Universität Wuppertal) und der Lehrstuhl für Elektromobilität und Energiespeichersysteme an der Universität Wuppertal.
Projektleitung: Prof. Volker Huckemann
Fördermittelgeber: Bundesministerium für Wirtschaft und Energie (BMWi)
Laufzeit: 03/2020 – 02/2025
Die Georg-August-Universität in Göttingen verwandelt ein im Denkmalschutz stehendes Universitätsgebäude aus dem 19. Jahrhundert in das "Forum Wissen", ein kombiniertes Lehr-, Forschungszentrum und Museum. Seit Januar 2020 wird das Gebäude umfassend renoviert, um seiner neuen Funktion gerecht zu werden, dabei aber sein historisches Erscheinungsbild zu bewahren.
Ein Schlüsselelement der Renovierung ist die Erfüllung der spezifischen Konservierungsanforderungen für das Raumklima des Museums. Um sich vor Sonneneinstrahlung zu schützen, ohne das äußere Erscheinungsbild des Gebäudes zu verändern, wird schaltbares Glas von Merck installiert. Diese Technologie gewährleistet eine natürliche Farbwiedergabe im Inneren und trägt zu einem geeigneten Klima für Ausstellungsstücke und Besucher bei, wobei das ursprüngliche Aussehen des Gebäudes erhalten bleibt.
Das Projekt umfasst die Erforschung des Pilotbetriebs von schaltbarem Glas in einem Museumsumfeld. Dies beinhaltet die Erfüllung klimatischer Anforderungen und die Bewertung der Energieunterschiede im Vergleich zu traditionellen Beschattungslösungen.
Der Erfolg des Projekts wird durch thermische Simulation gemessen. Hierbei wird die TRNSYS-Software verwendet, um einen Museumsabschnitt zu modellieren und das schaltbare Glas zu simulieren. Nach Validierung des Modells mit umfangreichen klimatischen und bautechnischen Parametern dient es als Grundlage für die Untersuchung des Pilotbetriebs des Glases und die Optimierung des technischen Betriebs des Museums.
Weitere Informationen zu diesem Projekt hier.
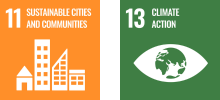
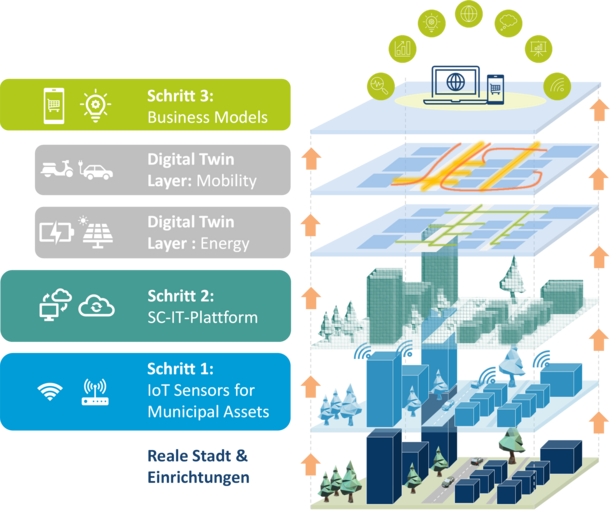
Projektleitung: Prof. Dr. Haydar Mecit
Fördermittelgeber: Bundesministerium für Bildung und Forschung, Programm FH-Impuls (Förderkennzeichen: 13FH0I93IA)
Laufzeit: 07/2022 – 12/2024
Ziel: Fortschritt und Umsetzung von Smart City-Anwendungsfällen in den Bereichen Smart Environment, Smart Mobility & Smart Energy als potenziell replizierbare Leitbilder.
Aufbauend auf früheren Studien entwickelt HpSCiLivLabs Teile eines Smart City-Forschungslabors als gemeinsamen Raum für verschiedene Stakeholder der Smart City. In diesen Workshops werden datengesteuerte Simulationen, Prototypen und Ansätze mit Digital Twins genutzt, um Teilnehmer aus verschiedenen Sektoren (wie Wissenschaft, Wirtschaft und Kommunalverwaltung) in einer innovativen Arbeitsumgebung zusammenzubringen.
Der Fokus liegt nun auf der Fertigstellung und Erweiterung von Smart City-Real Labs (hauptsächlich Sensoren und Daten aus städtischen Räumen), die zuvor für Tests und Validierungen eingerichtet wurden. Ein zentrales Element ist eine teilweise vorhandene und sich entwickelnde Smart City-IT-Plattform, die Datenquellen aus den Real Labs mit dem Forschungslabor verbindet. Diese Plattform wird die weitere Verarbeitung und Analyse von Daten erleichtern, um Smart City-Anwendungsfälle in den Bereichen Umwelt, Mobilität und Energie zu verbessern, unter Verwendung moderner Visualisierungs- und Kollaborationsmethoden.
Projektkonsortium:
- Hochschule Bochum, Institut für Elektromobilität und Labor für Nachhaltigkeit in der Technologie
- Fachhochschule Dortmund
- Westfälische Hochschule Gelsenkirchen, Institut für Internetsicherheit
Industrie- und öffentliche Institutionen:
- Stadtwerke Herne AG
- Straßenbahn Herne-Castrop-Rauxel GmbH
- Wirtschaftsförderungsgesellschaft Herne mbH
- Stadt Herne, Amt für Digitalisierung
Weitere Informationen zu dem Projekt hier.
Projektleitung: Prof. Dr.-Ing. Andrej Albert & Thilo Schmidt, M.Sc.
Fördermittelgeber: Bundesministerium für Wirtschaft und Klimaschutz (BMWK)
Laufzeit: 2022 – 2025
Kooperationspartner: Ruhr-Universität Bochum, RWTH Aachen, fischerwerke GmbH & Co. KG
Das Ziel der Initiative "air-Kon-Matrizen" besteht darin, aufblasbare, individuell geformte, ressourceneffiziente Hohlkammermatrizen für die Herstellung von Leichtbau-Fundamenten zu entwickeln. Diese Matrizen sollen in die Schalung von Fundamenten integriert werden, um überschüssigen Beton selektiv zu verdrängen und somit den Energieverbrauch und die damit verbundenen CO2-Emissionen erheblich zu reduzieren.
Die Verantwortung für die Optimierung der Form der Hohlkammermatrizen liegt beim Fachbereich Massivbau der Hochschule Bochum. Dies umfasst den rechnerischen Nachweis der Tragfähigkeit durch nichtlineare FEM-Simulationen und die Anwendung eines Algorithmus auf Grundlage genetischer Programmierung.
Eine schematische Darstellung einer 'air-Kon-Fundamentplatte' unter typischen Lastbedingungen mit maßgeschneiderten Hohlkammermatrizen ist in der beigefügten Abbildung dargestellt.
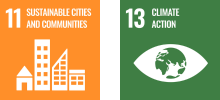
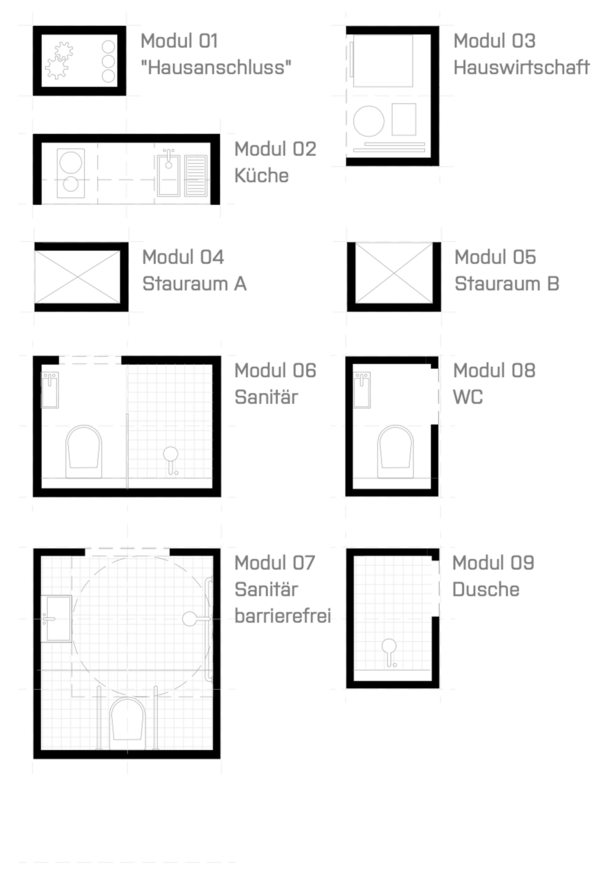
Projektleitung: Prof. Dr. Klaus Legner
Fördermittelgeber: Bundesministerium für Bildung und Forschung (BMBF)
Wer von Wohneigentum träumt, stellt sich Haus oder Wohnung häufig mitten in der Natur vor, abseits der Stadt. Das kann problematisch sein, denn: Im Rahmen der Zersiedlung dehnen sich Städte weiter aus, (Grün-)Flächen werden besetzt und es entsteht beispielsweise mehr Verkehr. Sinnvoller ist es, vorhandene Flächen in Quartieren zu nutzen und gute Wohnlösungen zu schaffen. Der „HABI-CORE“-Infrastrukturkern wird konzipiert für die Integration in leerstehende Bestandsgebäude und für kleine, brach liegende Baulücken in der Stadt. Auf diese Weise soll zusätzlicher kostengünstiger, bezahlbarer und barrierearmer Wohnraum im städtischen Raum entstehen. Im Rahmen des Projekts wird ein nachhaltiger Prototyp aus Holz entwickelt, gebaut und getestet und als begehbarer Prototyp in Bochum präsentiert.
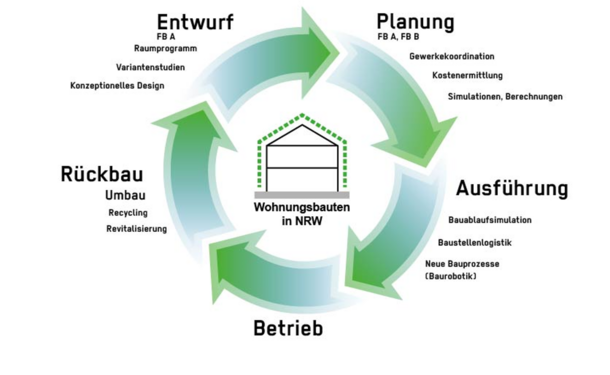
Projektleitung: Prof. Dr. Sven Pfeiffer
Der Aspekt der Nachhaltigkeit wird bei der Sanierung und Planung von Gebäuden immer wichtiger. Fragen lauten z. B.: Welche Form der Dämmung oder Heizung ist sinnvoller, sozialer, wirtschaftlicher? Damit Antworten bei der architektonischen Planung effizienter gefunden werden, arbeitet der Fachbereich Architektur an einer digitalen Planungsmethode, die Bauwerksdaten im Vorfeld modelliert.
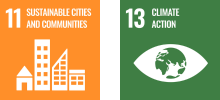
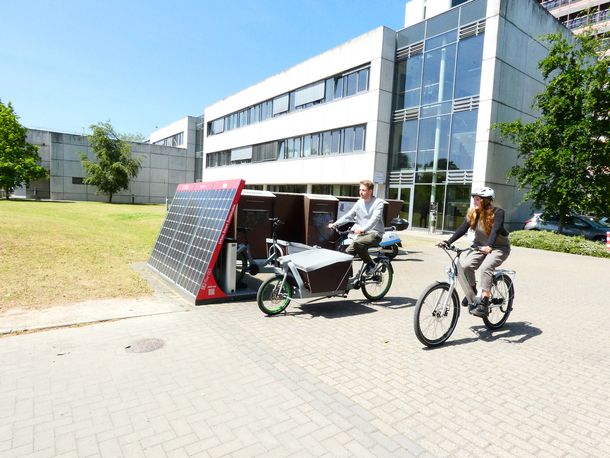
Projektleitung: Prof. Dr.-Ing. Semih Severengiz
Fördermittelgeber: Bundesministerium für Bildung und Forschung (BMBF)
Inzwischen prägen E-Scooter, E-Bikes und Co. das Straßenbild vieler Großstädte in NRW. Doch noch nicht für alle Bürger:innen ist die Nutzung der Fahrzeuge attraktiv. Dabei könnte die sogenannte E-Mikromobilität einen Beitrag zum Klimaschutz leisten, wenn Geschäftsmodelle nachhaltig und wirtschaftlich arbeiten. Wo liegen Probleme? Wie gelingt eine weitere Verbreitung vor allem in städtischen Randgebieten und was erhöht die Akzeptanz? Methoden wie z. B. räumliche Analysen, Befragungen von Bürger:innen und Reallabore sollen Antworten liefern. In Zusammenarbeit mit einem E-Fahrzeughersteller und Unternehmen für Batteriewechsel- und Solarladestationen werden neue Geschäftsmodelle erprobt und mit Hilfe von echten Nutzungsdaten bewertet. Das Projekt ist im Labor für Nachhaltigkeit in der Technik angesiedelt.